
86 17344894490
service@chalcoaluminum.com
車両製造における押出アルミニウムプロファイル構造部品
情報によると、欧州の機関車および自動車メーカーの既存の注文の約60%はアルミニウムボディを備えた車両です。20年前、そのような注文はわずか2%〜3%でした。現在、アルミニウム構造は、氷、tgv-2n、etr460、etr500、タルゴホテル列車、その他の高速列車、ならびに多くの郊外および都市鉄道輸送車両に適用されています。
押出アルミニウムプロファイル構造部品の採用は、1970年代初頭に始まりました。当時、アルミニウムプロファイルの適用における科学技術の進歩により、必要な形状とサイズに応じてアルミニウム部品を製造することが可能になりました。このアルミニウム部品は、英国のapt列車の傾斜車体に適用されています。しかし、当時、押出アルミニウム部品の適用は大きな利益をもたらさなかった、すなわち、より高い材料価格は製造作業負荷の軽減を補わなかった。当時、大型構造部品の使用により、車体の生産作業負荷は40%軽減され、全長26m車体の自重は7.5t、長さ26m鋼製車体の自重は11Tであった。1970年代、鉄道部門は、車両の耐用年数全体の総コスト(購入コストと運用および保守コスト)の計算にもっと注意を払いました。彼らは、列車の牽引エネルギーの消費は、車両の自重に大きく依存する同じレベルに維持されなければならないことに気付きました。
その後、1980年代半ばに最も重要ないくつかの新しい技術的および技術的対策が達成され、横方向固定の必要性を最小限に抑え、車両アルミニウムボディの生産時間をさらに短縮し、スチール車両と比較して50%削減した2層シェルの大型構造部品の押出法の採用など、 そして、従来の方法に従って二層シリンダーボディを作ることが可能であり、その後、窓穴の開放溶接作業はすべて、ロボット技術と機器を使用して部分的にのみ、統一された技術操作の過程で完了します。
現在、鉄道部門が新車の開発への参加を徐々に減らし、初期製造コストと将来の運用コストを削減するために購入ポリシーを実施すると、製造業者は加入者の技術的要件を満たし、市場の発展動向に適応するために新しい構造と材料を採用する自由度が高まります。押出アルミニウムプロファイル構造部品 は、車両構造に関するいくつかの厳しい要件を満たすという点で他の利点も有する。例えば、二重層シェル押出構造の剛性は、高速列車が出会うときに生じる空気力学的衝撃が特別な衝撃強度を有することを確実にすることができる。この構造の車体のもう一つの重要な特徴は、その大きな縦方向の剛性です。縦剛性と横剛性の比は70:30に達することができ、鋼鉄車体の比は40:60です。さらに、アルミニウムプロファイルは、フィラーの使用や多くの手作業なしで、良好な外部形状の要件を満たすこともできます。例えば、ドイツ連邦鉄道の一部のモデルでは、フィラーが使用されていないため、計算後、塗料コーティングとともに、自重は500kgにすることができます。
押出アルミニウムプロファイル構造部品の使用はまた、自動車メーカーが複雑な作業に直面するようにします。彼らは労働価格と材料価格のバランスを見つけ、デザイナーにこのバランスを達成するよう努力させなければなりません。材料は概念全体の1つの要素にすぎないことを明確にする必要があります。採用された生産プロセスと技術プロセスも、企業の生産能力に適合し、投資とのバランスをとるように詳細に策定する必要があります。
たとえば、ほとんどの機械製造会社にとって、生産手段の埋蔵量を最小限に抑えることは最優先事項です。設計者による材料とプロセスの選択は、これに大きな影響を与えます。ABBには、毎週アルミボディを搭載した8台の車両を生産できる生産ラインがあり、材料保管の総コストを8%削減します。しかし、このバランスは、材料の使用によって引き起こされる技術的プロセスの変化のために容易に破壊される。例えば、溶接から接合への移行が、接合硬化に必要なかなりの時間を補うために、より多くの日次埋蔵量を必要とする場合などです。
鉄道車両製造用のアルミニウムプロファイルのもう1つの大手サプライヤーは、ドイツのVAW会社です。同社のリーダーは、車両構造の標準化とモジュール設計方法の採用に大きな発展傾向があると予測しており(この傾向は市場の需要により強化されているため、メーカーの支持を得ています)、ドイツの地方鉄道輸送の地域化に対する市場の需要を考慮すると、 一部の民間企業は、個々の発注者の要件を満たすために標準化されたモジュール構造を使用することにもっと注意を払うでしょう。現在、ヨーロッパの様々な機関車メーカーや自動車メーカーが多数の設計アイデアを持っており、これらのアイデアはモジュール設計に基づいています。標準化とモジュール性へのこの変換は、生産者とユーザーの両方にとって有益です。自動車製造におけるアルミニウムプロファイルの使用の拡大は、自動溶接のより広範な使用のために生産サイクルを大幅に短縮する。
また、アルミ車体を溶接した車両は耐衝撃荷重性が高く、走行安全性の向上に資することも明らかです。ABBはアルミニウム構造物の破壊試験を組織し実施するために100万ポンドを投資し、満足のいく、そしてさらに重要なことに、期待される試験結果を得た。同社はまた、事故車両の故障方法の修復において貴重な実務経験を蓄積してきました。1994年初頭、フランスのGEC Alstomが発注したtgv-2n列車のダブルデッキ乗用車試験サンプルの損傷試験では、衝撃力が250tの場合、8mjの吸収された衝撃エネルギーのために構造が合計80cm押し出され、アルミニウムボディ全体がそのまま残っていることが証明されました。
同時に、アルミニウム車体の利点の認識は問題がないわけではありません。鋼体機関車および自動車メーカーは、ドイツの製氷列車の製造工程においてアルミニウムが重視されることに懸念を表明し、1994年に鋼の優位性を確認するための調査を実施しました。しかし、従来と同様に、鉄骨構造を用いると、車体の自重が約20%増加する。
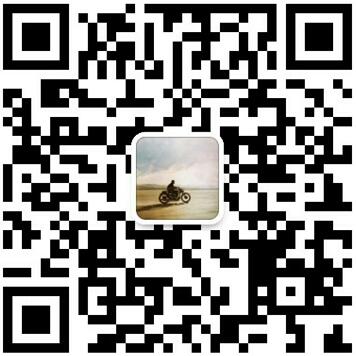
製品の無料提供は、いつでも相談へようこそ、私たちは最初の返信を与えます。私たちの電子メール: